On October 17, the "Thousand-Ton Scale Biomass Catalytic Conversion to Ethylene Glycol Pilot Technology," jointly developed by the team of Academician Zhang Tao, Researcher Zheng Mingyuan, and Researcher Wang Aiqin from the Catalysis and New Materials Research Center (Group 1500) of our institute, in collaboration with Zhongke Baiyijin (Zhengzhou) New Energy Technology Co., Ltd. (hereinafter referred to as "Zhongke Baiyijin Company"), passed the scientific and technological achievement evaluation organized by the China Petroleum and Chemical Industry Federation. Academician He Mingyuan of East China Normal University served as the chair of the evaluation committee, and Wang Xiujiang, Deputy Director of the Science and Technology Equipment Department of the China Petroleum and Chemical Industry Federation, presided over the meeting. Li Xianfeng, Deputy Director of our institute, and relevant personnel from research and administrative departments attended the meeting.
During the meeting, Wang Aiqin and Zheng Mingyuan presented the research report and the pilot work report, respectively. Professor Fu Yao from the University of Science and Technology of China, leader of the 72-hour assessment team, reported the on-site assessment results. The evaluation committee thoroughly reviewed the novelty search report and related evaluation materials and engaged in in-depth discussions with the research team and corporate partners. The committee unanimously concluded that the technology pioneered a novel one-step catalytic conversion route from biomass sugars to ethylene glycol, developed a complete thousand-ton-scale biomass-to-ethylene glycol process, and achieved a leap from fundamental research discoveries to large-scale application. The integrated technical level reached internationally leading standards, and the evaluation was unanimously approved.
Post-Evaluation Press Conference
Following the evaluation, our institute held a press conference for the "Thousand-Ton Scale Biomass Catalytic Conversion to Ethylene Glycol Pilot Technology," chaired by Li Xianfeng. Journalists from media outlets including Xinhua News Agency, China Media Group, Economic Daily, China Daily, Science and Technology Daily, China News Service, China Youth Daily, China Science Daily, China Education Television, People’s Daily Online, Guangming Online, China.org.cn, Outlook, China Chemical Industry News, Beijing Radio and Television Station, and The Beijing News attended the event. During the conference, journalists exchanged questions with evaluation committee experts, research team members, and corporate representatives.
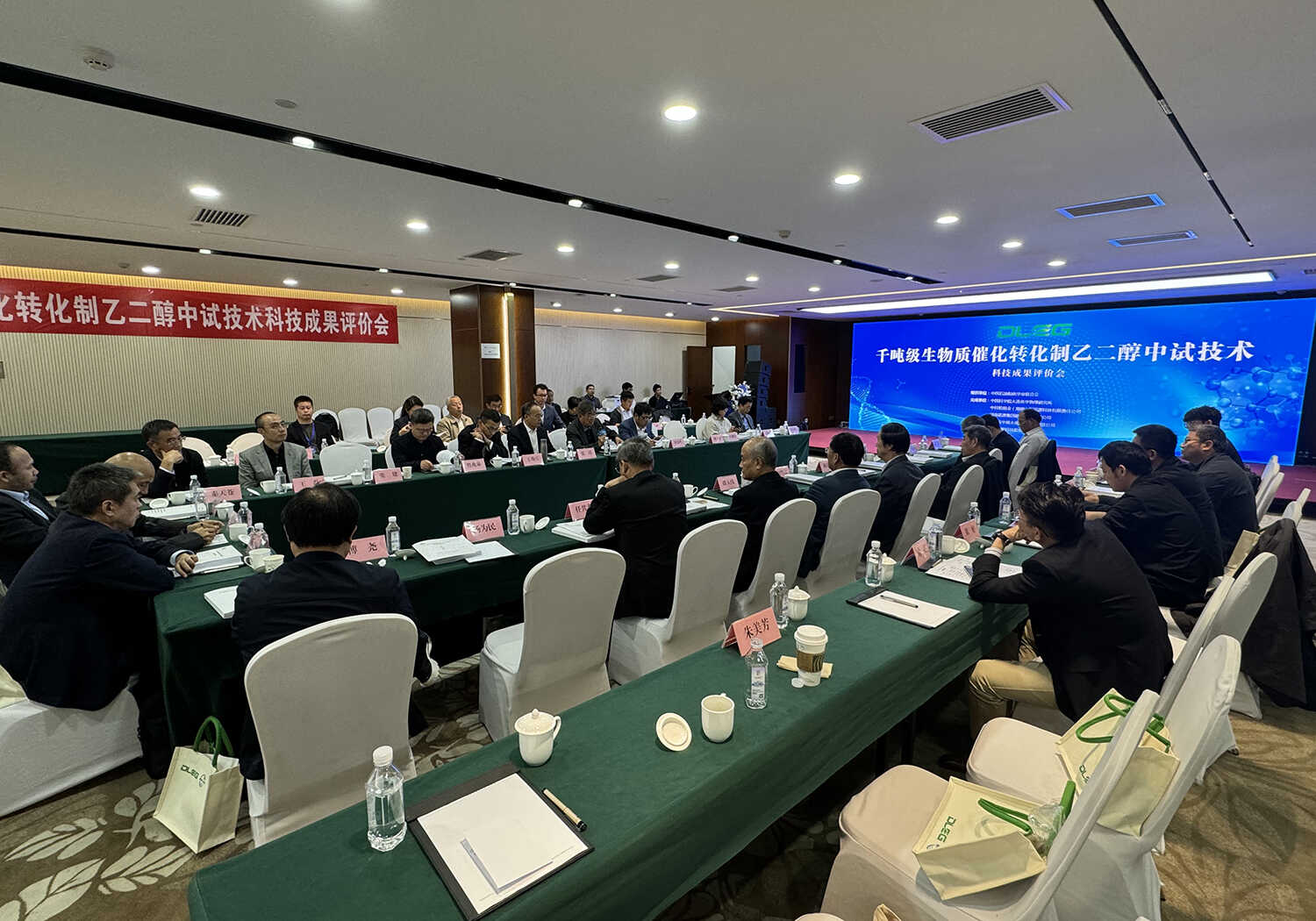
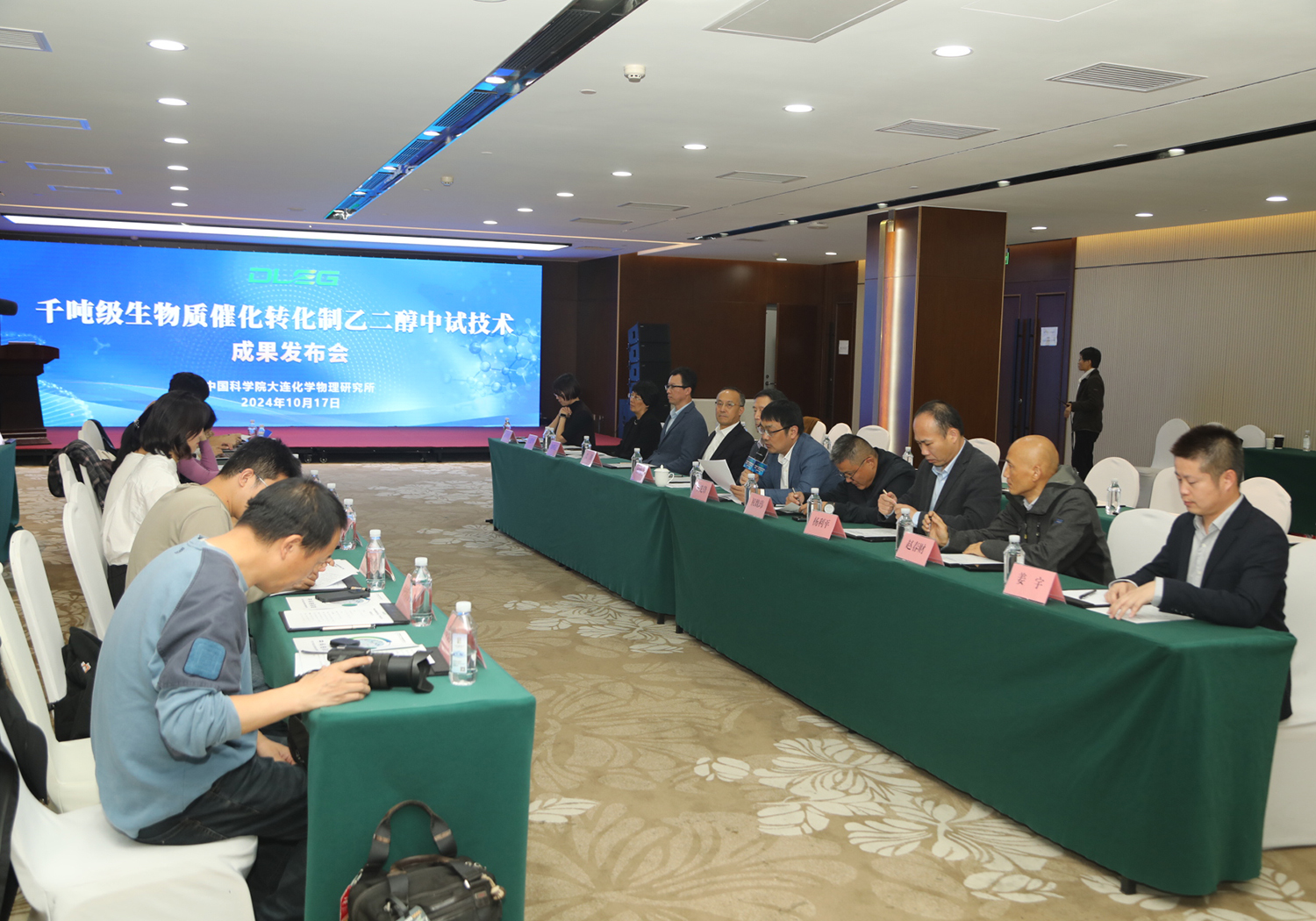
Background and Significance
Ethylene glycol (EG) is a critical bulk energy chemical, with global annual consumption exceeding 30 million tons, primarily used in producing polyester fibers, polyester bottle chips, antifreeze, coatings, and pharmaceuticals. China, as the world’s largest EG consumer (over 20 million tons annually), currently relies on petroleum-derived ethylene or coal as feedstocks, which face challenges such as non-renewable resources, high carbon emissions, and energy intensity. Developing green EG production technologies is urgently needed.
Research Milestones
2008: Zhang Tao’s team pioneered the direct catalytic conversion of cellulose to EG, establishing a new pathway for bio-based EG production.
2019: Collaboration with Zhongke Baiyijin Company launched the "Thousand-Ton Scale Biomass-to-EG Pilot Project."
2022: The world’s first thousand-ton-scale biomass-to-EG demonstration plant was built in Puyang, Henan, achieving industrial-grade EG production in June 2022.
2023: After technical upgrades, the plant completed a 72-hour on-site assessment on October 16, 2023, demonstrating 80% EG selectivity, 99.9% product purity, and UV transmittance meeting national polyester-grade standards.
Technical Advantages
Feedstock: Utilizes biomass such as straw sugars.
Process: Short route, mild conditions, high atom economy, and full intellectual property (48 authorized invention patents, 12 PCT international patents).
Performance: Outperforms existing bio-ethanol-based routes in technical-economic efficiency; EG quality surpasses coal-derived products in polyester synthesis tests.
Strategic Impact
This technology provides a green, low-carbon circular economy pathway for EG production, supporting China’s "Dual Carbon" goals and sustainable development. The bio-based EG has been commercialized for producing bio-polyester (PET), fully bio-based furan plastics (PEF), and fragrances. The pilot success lays the foundation for 10,000-ton industrial deployment, offering critical solutions for upgrading the EG industry chain, advancing bio-polyester production, and promoting green chemical manufacturing.
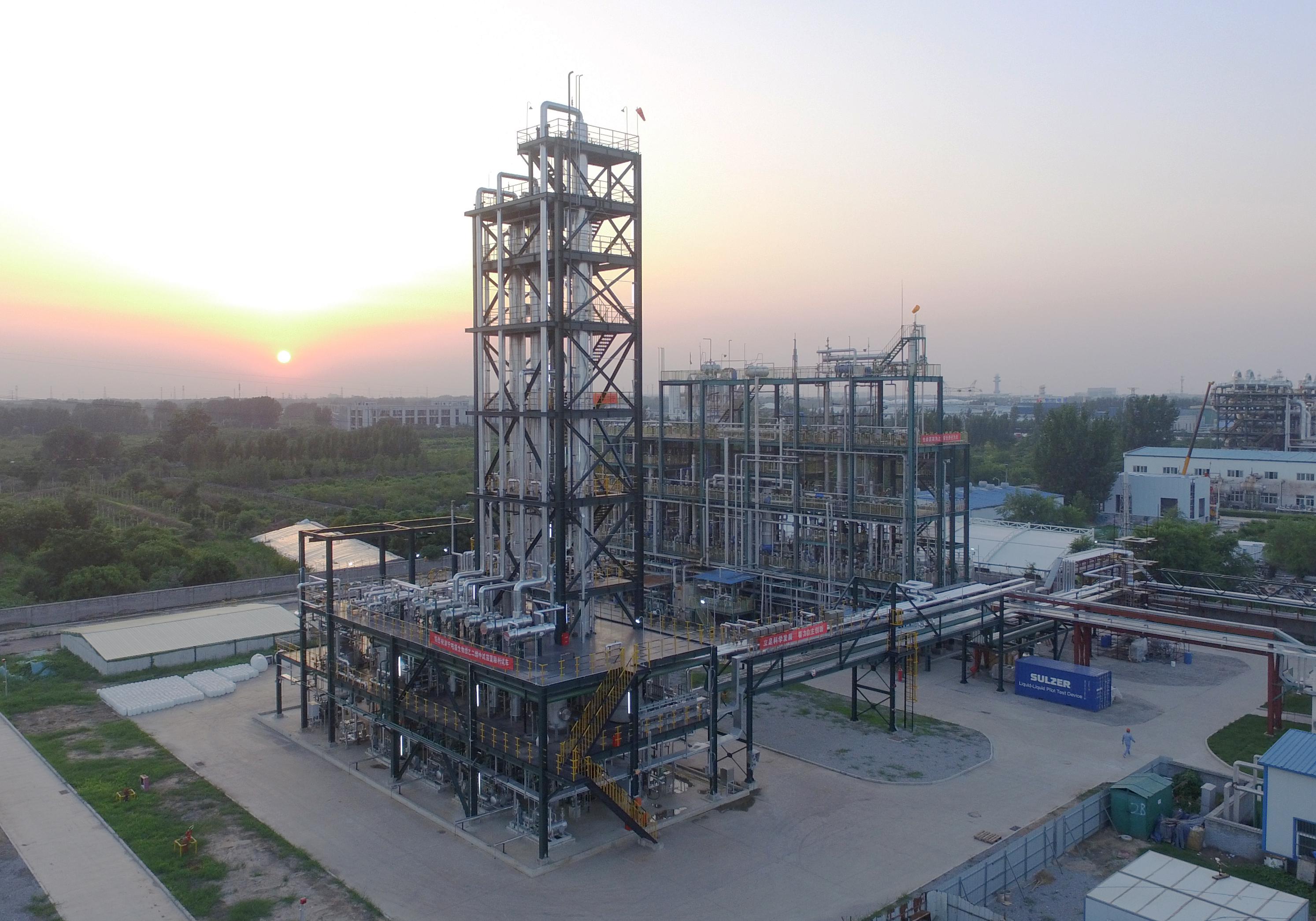